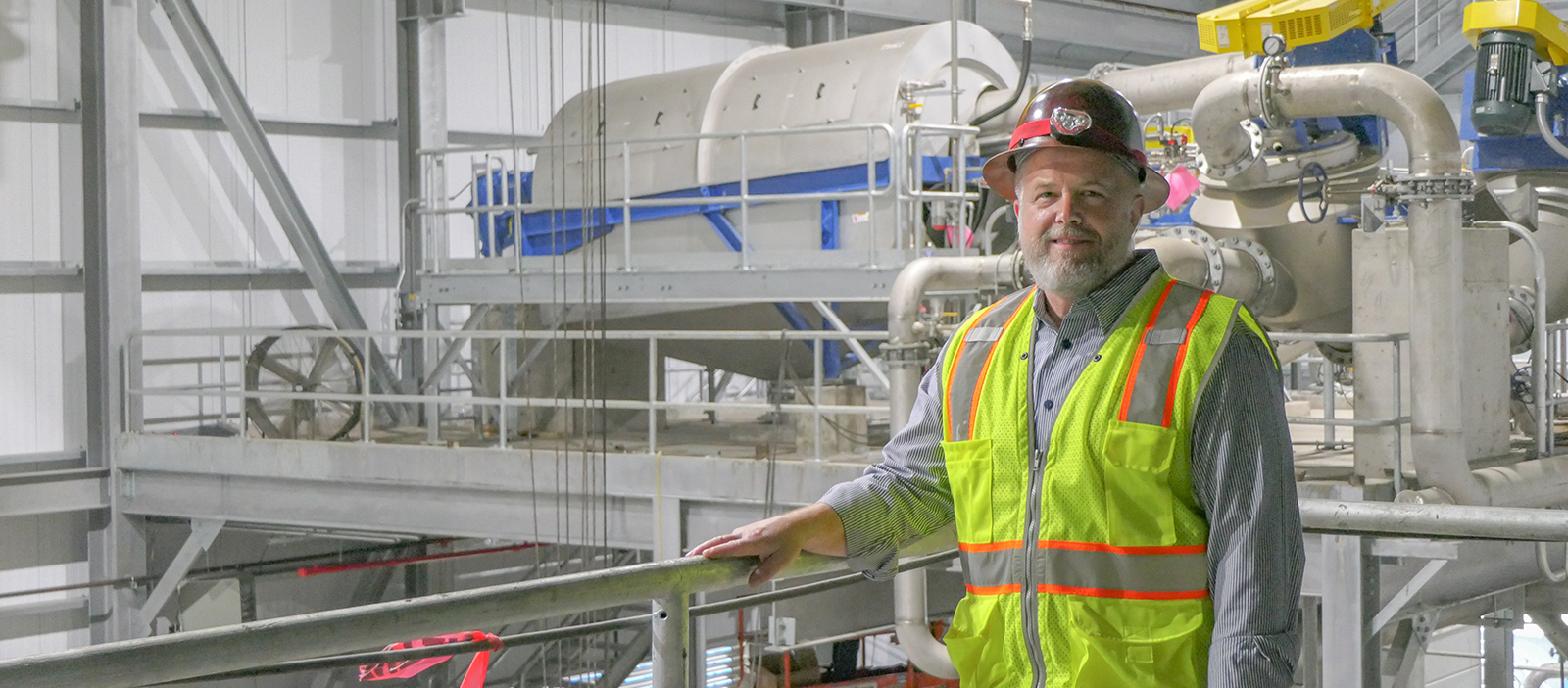
Kevin Haney no puede escapar del papel. Está en las fibras de su maquillaje, por así decirlo. Kevin, gerente regional de fabricación de Sonoco para la División de Papel, se ha trasladado por la compañía durante sus 30 años de antigüedad, ocupando puestos en Papel, Reciclaje y Operaciones, pero su afecto por el papel y su historia lo trajo de regreso a un puesto de liderazgo en su división original. Es un puesto en el que Kevin asume una enorme responsabilidad y satisfacción, ya que su padre y su abuelo trabajaron en fábricas de papel. No solo disfruta del trabajo diario, sino que se enorgullece del legado que vive y deja a las comunidades.
Hoy en día, una de las principales responsabilidades de Haney es gestionar el Proyecto Horizon, un compromiso para transformar la máquina mediana corrugada de Sonoco (máquina n.o 10 ) en Hartsville, S.C., en una operación de cartón reciclado sin recubrimiento (URB) de última generación con una capacidad de producción anual de 180,000 toneladas. La nueva máquina fue diseñada con el objetivo de ser el productor de URB más grande y de menor costo del mundo. Se espera que el Proyecto Horizon se complete al final del segundo trimestre de 2022.
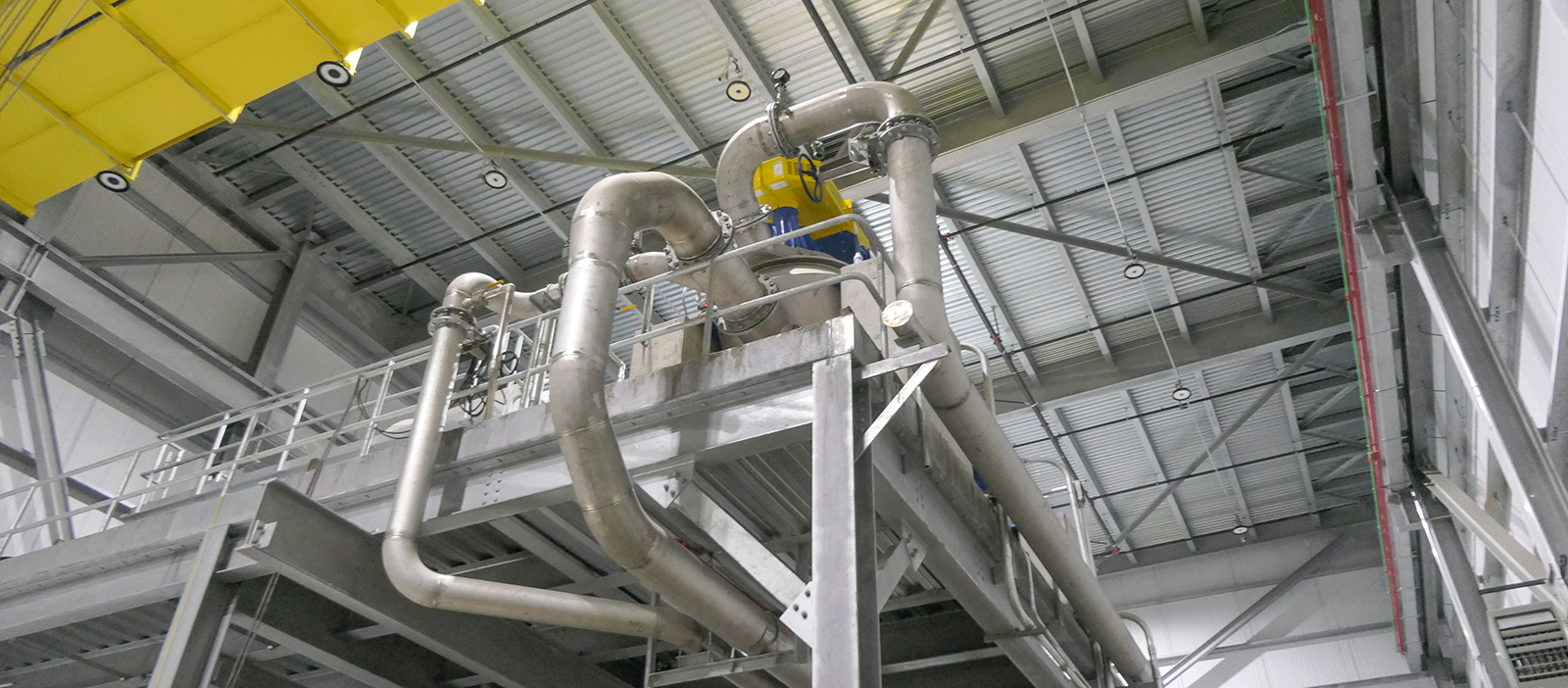
Hablamos con Kevin para obtener más información sobre su viaje en Sonoco y el liderazgo del Proyecto Horizon.
¿Puede contarnos un poco sobre usted y su historia en Sonoco?
Es una historia bastante simple. Sonoco es la primera y única compañía para la que he trabajado desde mi graduación en la Universidad Estatal de Carolina del Norte. He estado en Sonoco durante 30 años, 28 de los cuales han estado en la sede central en Hartsville, S.C. Comencé en la División de Papel y ascendí a un puesto de gerente. Desde allí, fui a la División de Reciclaje como Gerente Regional, luego Director de Operaciones, pero extrañaba tanto la División de Papel que volví después de unos años. Hoy, como gerente regional de fabricación de la División de Papel, tengo responsabilidades en las operaciones de Hartsville y en las operaciones de Richmond, Virginia.
Usted forma parte de la gestión de Project Horizon. ¿Podría decirnos cómo surgió el proyecto?
Project Horizon es parte de nuestro Sistema de optimización de activos de América del Norte y es la fase dos. La fase uno implicó mejoras a nuestras fábricas de nivel uno, que son nuestras fábricas más rentables y de menor costo. En el momento de la fase uno, nuestro ahora director ejecutivo, Howard Coker, era el vicepresidente ejecutivo de la División Industrial Global. Se acercó a nosotros para preguntarnos cuál sería la siguiente fase. Sabíamos que la siguiente fase sería abordar una operación antigua aquí en Hartsville. Los costos estaban aumentando, y estábamos investigando la posibilidad de tener que apagar algunas de las máquinas más antiguas y de mayor costo. Si no hiciéramos algo, probablemente tendríamos que apagar el N.o 10 , así como algunas otras máquinas. La gerencia del papel se reunió y tuvimos que tomar algunas decisiones.
Originalmente, analizamos este proyecto para reconstruir la máquina n.o 10 en Hartsville en 2005 cuando nuestro socio nos notificó sobre los planes de no renovar el contrato de empresa conjunta. Nadie estaba demasiado entusiasmado por tener que gastar ese tipo de dinero en ese entonces, así que cuando Howard pidió nuestros planes de la fase dos, decidimos que era hora de convertir la máquina n.o 10 en una máquina URB, que es lo que fabrica el resto de nuestro sistema de molienda. Esta conversión convertiría a la máquina n.o 10 en el productor de URB más grande y de menor costo del mundo y aseguraría el futuro del complejo Hartsville durante los próximos 50 años. Entonces, lo que estamos haciendo es convertir la máquina n.o 10 en una máquina de cartón 100 % reciclada. Actualmente, utiliza 50/50 fibras de madera dura recicladas y vírgenes para producir un medio corrugado, que es lo que se utiliza en las cajas de cartón.
URB de fabricación requerirá el reemplazo y la adición de nuevos activos a la máquina actual para permitir la fabricación de grados de papel URB actuales para nuestros grados de toallas y tejidos livianos a grados de tubos y núcleos de mayor peso. Esta máquina está diseñada para producir un amplio espectro de grados. Project Horizon también está incorporando un nuevo almacén de 109,000 pies cuadrados que albergará dos bobinadoras sin conexión para cortar el papel que sale de la máquina n.o 10 .
Entonces, ¿cómo se volvió responsable de administrar el Proyecto Horizon?
Bueno, como gerente regional, el complejo Hartsville se encuentra bajo mis responsabilidades, pero también tengo mucha experiencia con la máquina de papel N.o 10 . La mayor parte de mi carrera se ha dedicado a esa máquina. Mi conocimiento y experiencia encajan bien con la expectativa de que asumiría parte del liderazgo de este proyecto.
He podido dividir a mi equipo en dos grupos, y la mitad se centró en Project Horizon, dirigido por Jonathon Saleeby, y el resto gestiona las operaciones diarias, dirigido por Jonathon Anderson. Por lo tanto, ha sido un desafío para todos asumir nuevas responsabilidades. Curiosamente, encontré una cita de 1994 donde investigamos por primera vez la actualización de esta máquina. Eso siempre ha sido un sueño mío llevarlo al siguiente nivel, y estoy muy emocionado de que finalmente suceda.
¿Hay algo específico en sus antecedentes que lo haya preparado para esto?
¡Nada! Quiero decir, tengo experiencia con la máquina n.o 10 , pero nada me preparó completamente para esto. Ha sido muy desafiante. Se necesita un ejército de personas para manejar un proyecto de este tamaño. Con un complejo de 100 años y máquinas de 70 años, cada vez que recoges una cucharada de suciedad, no sabes lo que podrías descubrir. Encontramos una botella de Coca-Cola que era marrón y tenía una fecha 1915 .
¿Cómo atraviesa los desafíos que surgen en un proyecto tan grande?
Es un enfoque de equipo. Tenemos muchas personas buenas involucradas. Son muchas reuniones y mucha “gestión del caos”, como lo llamamos, manejar lo que surge a diario. Los problemas de entrega probablemente han sido uno de nuestros mayores desafíos. Esto era algo que ninguno de nosotros esperaba. Además, el clima afecta casi todo lo que hacemos. Se suponía que debíamos verter la primera losa de concreto para el almacén la misma semana en que se previó que vendría un huracán. Tuvimos que averiguar cómo aumentar el cronograma unos días para reducir el impacto de posibles lluvias intensas en todo el trabajo realizado hasta ese momento. Hemos tenido que involucrar a muchas personas para intentar mantener todo encaminado.
¿Qué ofrece este proyecto en términos de mejoras de sostenibilidad?
Estamos pasando de producir nuestro producto de fibras de madera dura 50 % virgen a fibras 100 % recicladas. Eliminar esta fábrica de pulpa virgen definitivamente ayuda desde un punto de vista ambiental, ya que podemos eliminar la operación de fabricación de pulpa así como nuestra operación de recuperación química. Esto conduce a reducciones de gases de efecto invernadero y reducciones de agua dulce.
También estamos tratando de ser sostenibles durante el proceso de construcción real. Estamos reciclando mucho concreto y materiales de la demolición que volverán a la construcción del área de patio entrante.
¿Cuál es el impacto del proyecto en la comunidad?
Lo más importante es que, como he mencionado, la reconstrucción garantizará que el complejo de Hartsville mantenga la estación aquí y sea competitivo durante los próximos 50 años. Tiene más de 100 años ahora, y realmente no hay razón por la que no pueda seguir otros 100 años.
También hemos intentado enfocarnos en utilizar proveedores y contratistas locales para el proyecto tanto como sea posible. A la fecha, nos hemos comprometido a gastar 25 millones de dólares en el condado de Darlington y 50 millones de dólares en total en Carolina del Sur. Nos hemos reunido con los líderes de la ciudad y nos han dicho que la capacidad del hotel es del 95 % con todos los contratistas que tenemos aquí. Los restaurantes también están en auge. A la vez, tuvimos hasta 500 contratistas en el sitio, y ahora estamos promediando alrededor de 100 a 150 contratistas por día.
¿Qué lo motiva a usted y a su equipo?
Soy muy afortunado de tener un grupo sólido de personas trabajando conmigo en este proyecto. Todos comprendemos su importancia y el impacto que tiene en la compañía y la comunidad. Personalmente, para mí, la máquina n.o 10 fue donde empecé mi carrera en Sonoco, y es donde aprendí cómo funcionan las operaciones y cómo convertirme en líder. Debido a eso, tengo mucha propiedad y orgullo de querer que esta operación pase al siguiente nivel.
Tenemos varias generaciones de personas y familias que han trabajado en la División de Papel en Hartsville, y quiero ver que eso continúa. Vengo de una pequeña ciudad donde mi papá trabajaba en una fábrica de papel y su papá lo hacía y así sucesivamente. Hartsville me recuerda mucho dónde crecí, y quiero ver que la experiencia generacional continúa. Mi equipo comprende el impacto que tiene la papelera en la ciudad y la comunidad. Conocen la importancia de este proyecto y que se hace correctamente para tener un impacto positivo en el futuro de las personas, la comunidad y el medio ambiente.